Izbor površinskog obrade problem je s kojim se suočava svaki dizajner. Na raspolaganju su mnoge vrste mogućnosti površinskog liječenja, a dizajner na visokoj razini ne samo da bi trebao razmotriti ekonomiju i praktičnost dizajna, već i obratiti pažnju na proces montaže, pa čak i zahtjeve za okoliš. Ispod je kratak uvod u neke uobičajeno korištene premaze za pričvršćivače na temelju gornjih principa, za referencu praktičara učvršćivača.
1. Elektrogalvanizacija
Cink je najčešće korišteni premaz za komercijalne pričvršćivače. Cijena je relativno jeftina, a izgled je dobar. Uobičajene boje uključuju crnu i vojnu zelenu. Međutim, njegova performansi protiv korozije su prosječni, a njegove performanse protiv korozije najniži su među slojevima za oblaganje cink (premaznih). Općenito, ispitivanje pocinčanog čelika neutralnog soli provodi se u roku od 72 sata, a posebna sredstva za brtvljenje također se koriste kako bi se osiguralo da test neutralne soli traje više od 200 sati. Međutim, cijena je skupa, što je 5-8 puta veća od uobičajenog pocinčanog čelika.
Proces elektrogalvaniziranja sklon je zamljenju vodika, tako da se vijci iznad stupnja 10.9 uglavnom ne tretiraju s galvanizacijom. Iako se vodik može ukloniti pomoću pećnice nakon obloge, pasivizacijski film bit će oštećen na temperaturama iznad 60 ℃, tako da se uklanjanje vodika mora provesti nakon elektropleta i prije pasivacije. To ima lošu operatibilnost i visoke troškove obrade. U stvarnosti, opće proizvodne biljke ne uklanjaju vodik, osim ako ih određeni kupci ne mandate.
Konzistentnost između okretnog momenta i sile zatezanja pocinčanih pričvršćivača je loša i nestabilna, a oni se uglavnom ne koriste za povezivanje važnih dijelova. Da bi se poboljšala konzistencija unaprijed zakretnog momenta, metoda prekrivanja tvari pod mazivom nakon opterećenja također se može upotrijebiti za poboljšanje i poboljšanje konzistencije unaprijed zakretnog momenta.
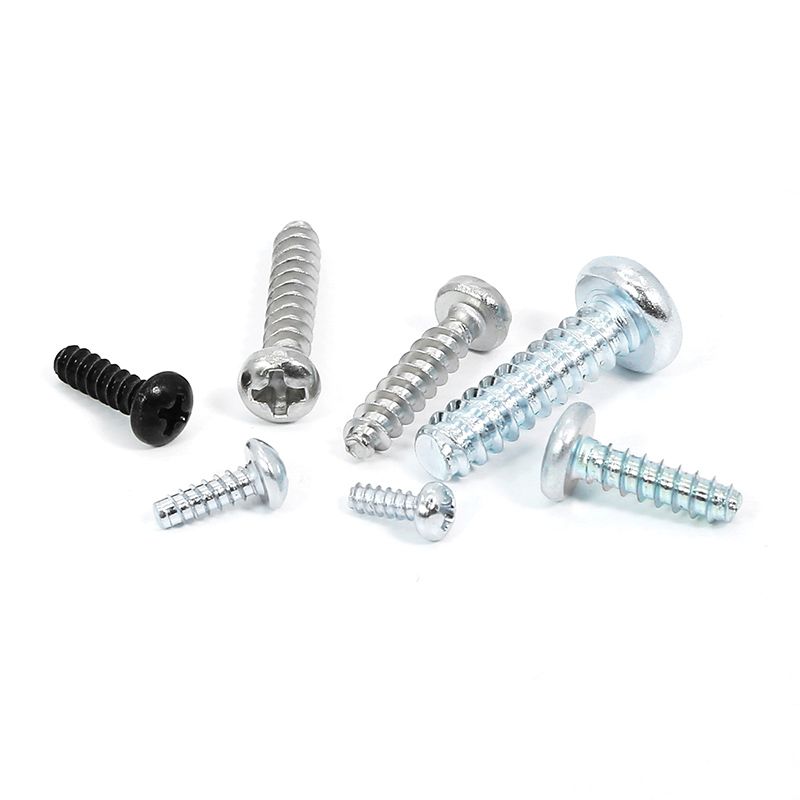
2. fosfatiranje
Osnovni princip je da je fosfatiranje relativno jeftinije od galvanizacije, ali njegova korozijska otpornost je gora od galvaniziranja. Nakon fosfacije, ulje treba nanositi, a njegov otpor korozije usko je povezan s performansama primijenjenog ulja. Na primjer, nakon fosfacije, nanošenje općeg ulja protiv hrđe i provođenje neutralnog ispitivanja prskanja soli samo 10-20 sati. Primjena visokokvalitetnog ulja za hrđanje može potrajati do 72-96 sati. Ali njegova cijena je 2-3 puta veća od općeg fosfativnog ulja.
Postoje dvije najčešće korištene vrste fosfacije za pričvršćivače, fosfatiranje na bazi cinka i fosfatiranje na bazi mangana. Fosfatiranje na cinku ima bolje performanse podmazivanja od fosfacije na bazi mangana, a fosfatiranje na bazi mangana ima bolju otpornost na koroziju i otpornost na habanje od cink -obloga. Može se koristiti na temperaturama u rasponu od 225 do 400 stupnjeva Fahrenheita (107-204 ℃). Posebno za povezivanje nekih važnih komponenti. Kao što su priključni vijci i matice motora, glava cilindra, glavni ležaj, vijci zamašnjaka, vijci i matice na kotačima, itd.
Vijci visoke čvrstoće koriste fosfatiranje, što također može izbjeći probleme s vodikom. Stoga, vijci iznad stupnja 10,9 u industrijskom polju uglavnom koriste površinsku obradu fosfatiranja.
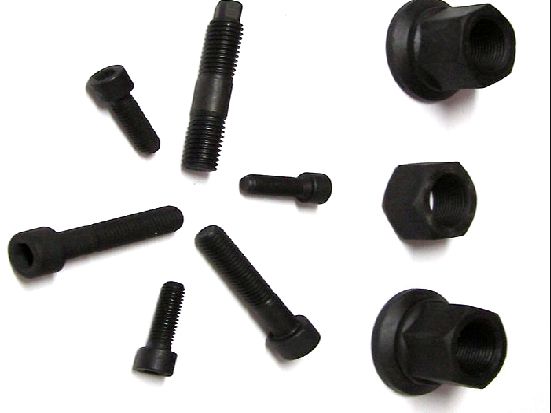
3. Oksidacija (pocrnjelo)
Blaching+Oilling je popularni premaz za industrijske pričvršćivače jer je najjeftiniji i izgleda dobro prije potrošnje goriva. Zbog crpljenja, gotovo da nema sposobnost prevencije hrđe, pa će brzo zahrđati bez ulja. Čak i u nazočnosti ulja, test spreja za sol može trajati samo 3-5 sati.
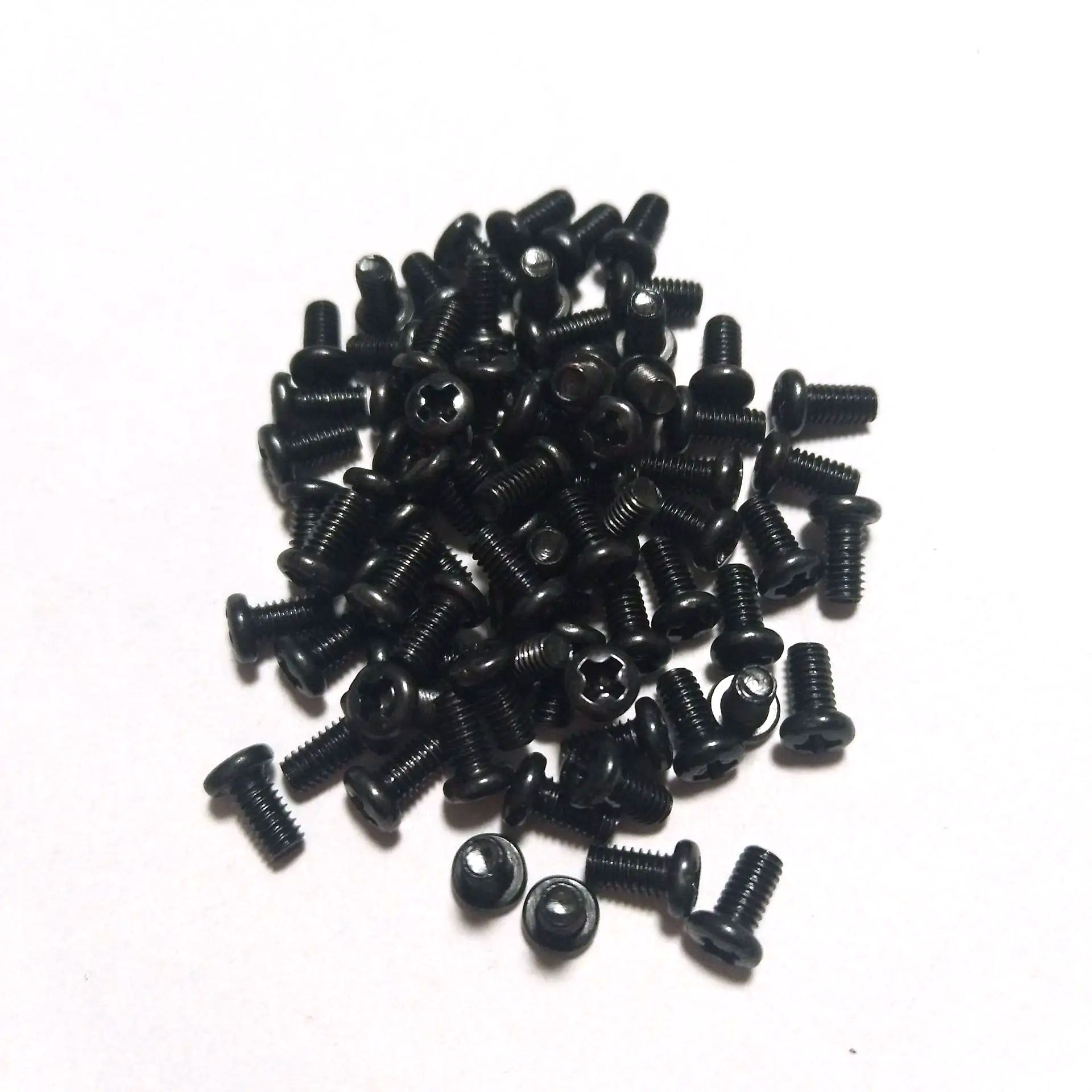
4.
Kadmijsko oblaganje ima izvrsnu otpornost na koroziju, posebno u morskom atmosferskom okruženju, u usporedbi s drugim površinskim tretmanima. Troškovi tretmana otpadne tekućine u procesu kadmija za elektroelekciju su visoki, a cijena mu je oko 15-20 puta veća od cinka. Dakle, ne koristi se u općim industrijama, samo za određeno okruženje. Pričvršćivači koji se koriste za platforme za bušenje nafte i zrakoplove HNA.
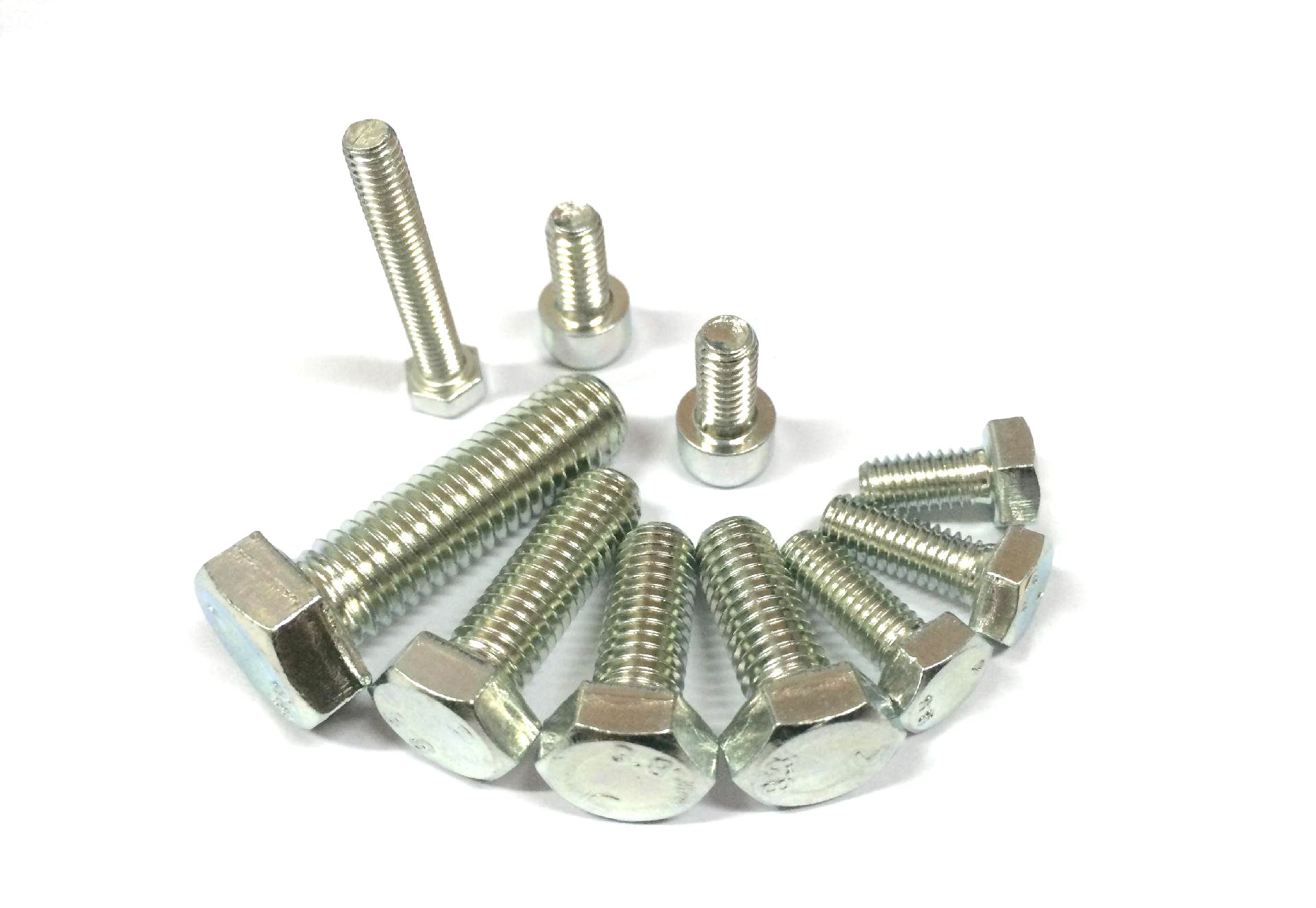
5. Krom za oblaganje
Kromov premaz je vrlo stabilan u atmosferi, nije lako promijeniti boju i izgubiti sjaj, a ima visoku tvrdoću i dobru otpornost na habanje. Upotreba kroma na pričvršćivačima uglavnom se koristi u ukrasne svrhe. Rijetko se koristi u industrijskim poljima s visokim zahtjevima otpornosti na koroziju, jer su dobri kromirani pričvršćeni učvršćivači podjednako skupi kao nehrđajući čelik. Tek kada čvrstoća od nehrđajućeg čelika nije dovoljna, umjesto toga se koriste kromirani učvršćivači.
Da bi se spriječila korozija, bakar i nikl prvo treba postaviti prije kromiranja. Kromov premaz može podnijeti visoku temperaturu od 1200 stupnjeva Fahrenheita (650 ℃). No, postoji i problem umiješanja vodika, sličan elektrogalvaniziranju.
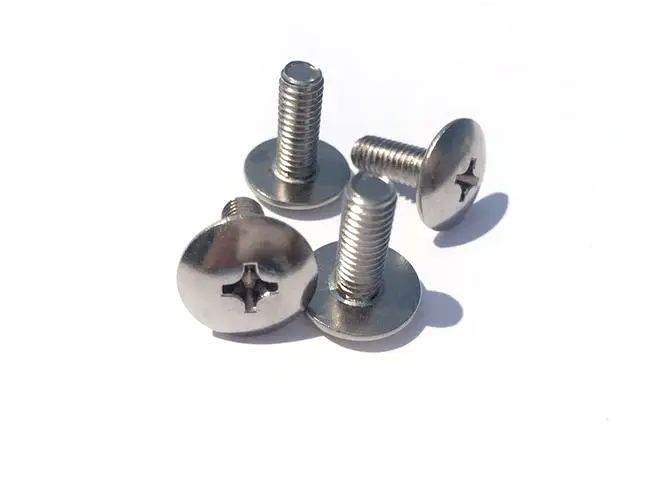
6. Nikalska obloga
Uglavnom se koriste u područjima koja zahtijevaju i antikoroziju i dobru vodljivost. Na primjer, odlazni terminali baterija za vozila.
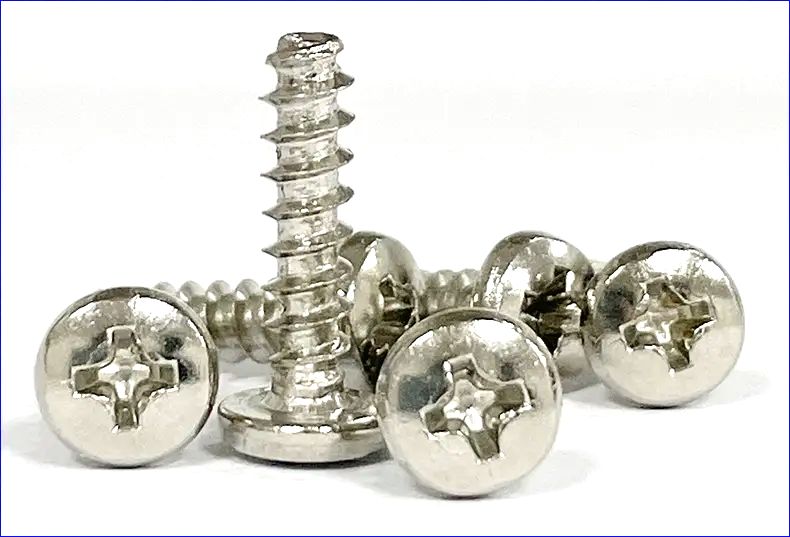
7. Vruće galvaniziranje
Vruće pocinčanike je toplinski difuzijski premaz cinka zagrijanog u tekućinu. Debljina premaza je između 15 i 100 µm. I nije lako kontrolirati, ali ima dobru otpornost na koroziju i često se koristi u inženjerstvu. Tijekom postupka pocinčavanja vrućeg uranjanja, postoji ozbiljno zagađenje, uključujući cinkov otpad i paru cinka.
Zbog debelog premaza uzrokovao je poteškoće u pričvršćivanju unutarnjih i vanjskih niti u učvršćivačima. Zbog temperature prerade pocinčanih pocinčaka, ne može se koristiti za pričvršćivače iznad stupnja 10,9 (340 ~ 500 ℃).
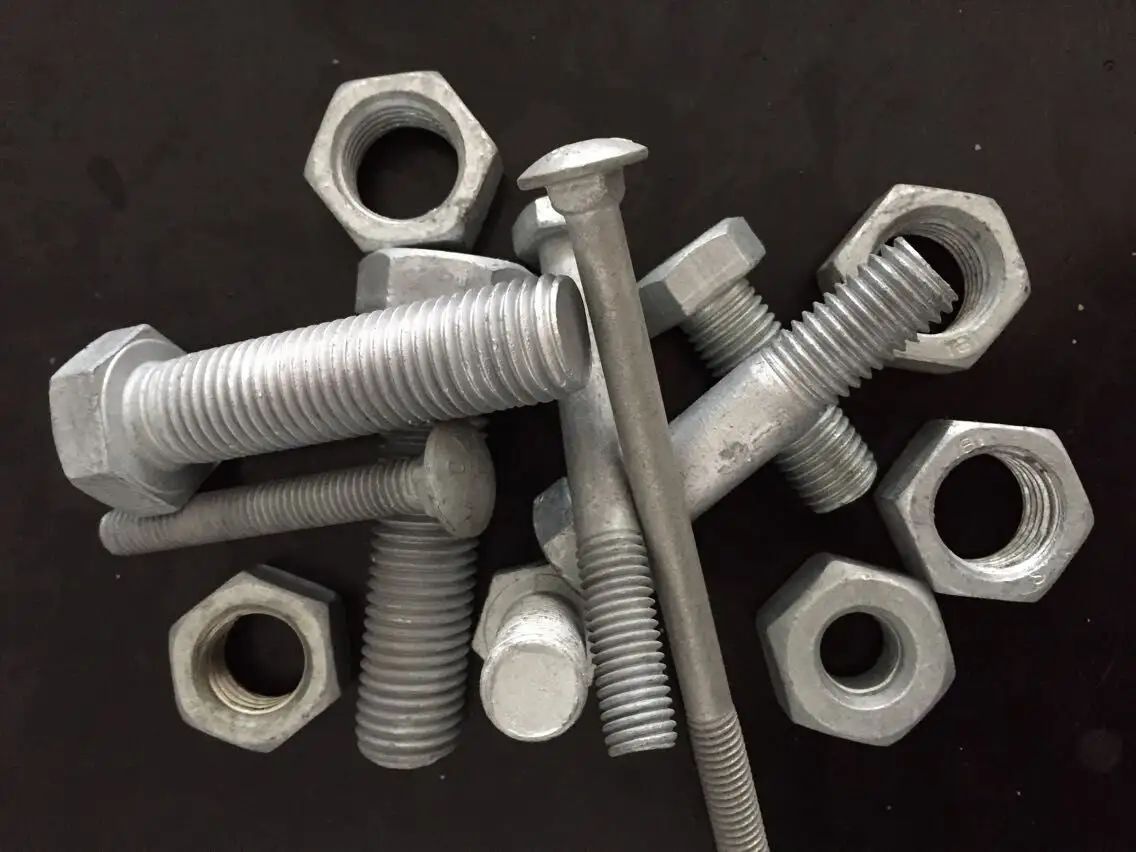
8. infiltracija cinka
Infiltracija cinka je čvrsta metalurška toplinska difuzijska prevlaka cinkovog praha. Njegova ujednačenost je dobra, a ujednačeni sloj može se dobiti i u nitima i slijepim rupama. Debljina obloge je 10-110 µm. A pogreška se može kontrolirati na 10%. Njegova čvrstoća vezanja i performanse antikorozije s supstratom su najbolji u prevlaci s cinkom (poput elektrogalvaniziranja, galvaniziranja s vrućim nagibom i DacroMet). Njegov postupak obrade je bez zagađenja i najprikladniji.
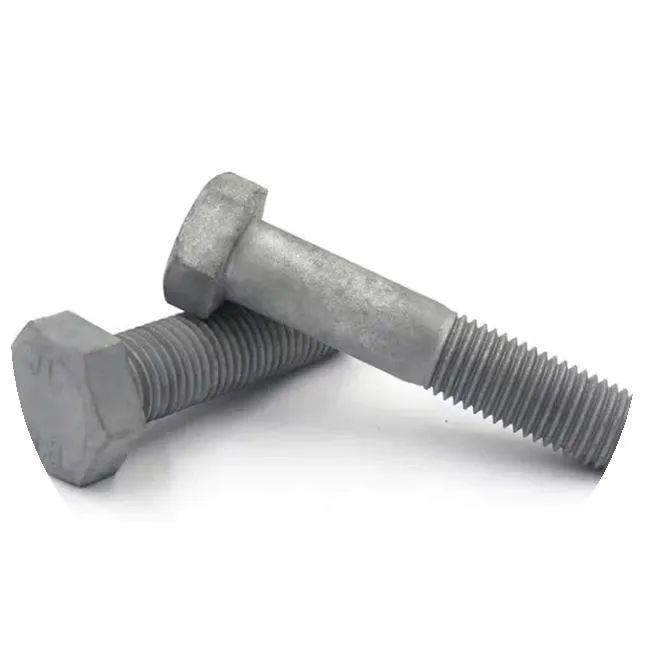
9. Dacromet
Ne postoji problem s vodikom, a performanse konzistentnosti za okretni moment vrlo su dobre. Bez razmatranja problema s kromom i okolišem, Dacromet je zapravo najprikladniji za pričvršćivače visoke čvrstoće s visokim zahtjevima za antikorozijom.
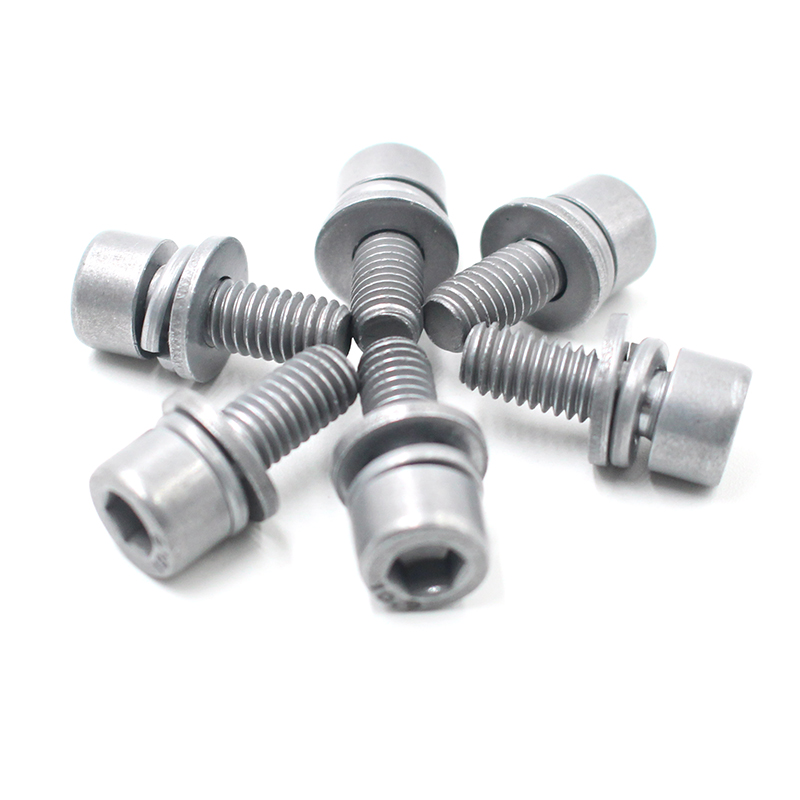
Post Vrijeme: svibanj-19-2023